”煤炭工人穿著白襯衫,在地面上很體面的采煤!“這是所有煤炭人的夢想。
現在,這個幾代煤炭人期待的井下“無人化”開采的夢想,在有些地方已經成為現實。
煤炭產業開采技術歷經了人力、炮采、普采、綜采,直至由機械化向自動化的轉型升級,現在逐步進入智能化無人開采時代。
今年,中國煤炭工業協會會長王顯政曾多次表示,我國已經建成“有人巡視、無人值守”智能化開采工作面47個!
下面是來自山西、陜西、內蒙古、山東、寧夏、安徽……六個省份,十座煤礦的智能化開采情況,一起來了解一下,看看無人化開采到底什么樣兒!
注:隨機排名,不分先后
01 黃陵一號煤礦
陜煤集團黃陵礦業有限公司下屬的核心骨干礦井,年生產煤炭600萬噸。
說到智能化開采,黃陵一號煤礦就不得不提。
幾年前黃陵一號煤礦就開始了國產綜采裝備智能化無人開采技術研究。
2014年5月該礦就實現了1.4至2.2米較薄煤層智能化綜采,年產200萬噸;2015年9月實現了中厚煤層智能化綜采工作面,年產400萬噸,在國內率先實現了地面遠程操控采煤的常態化。
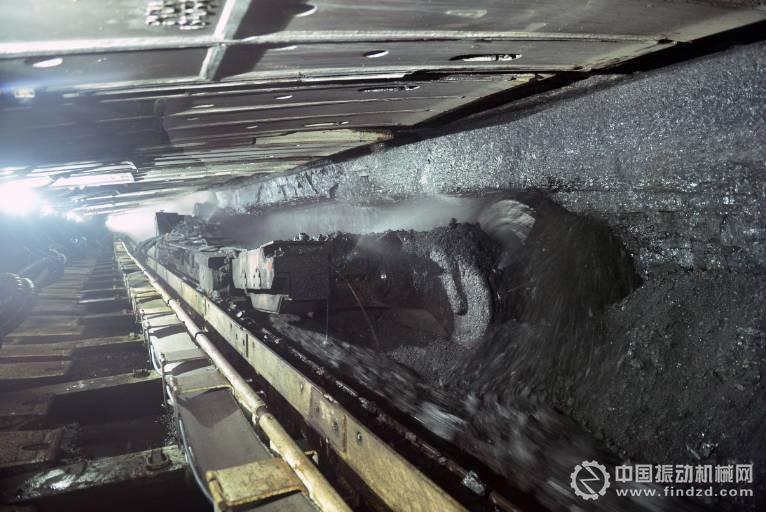
采煤工作面
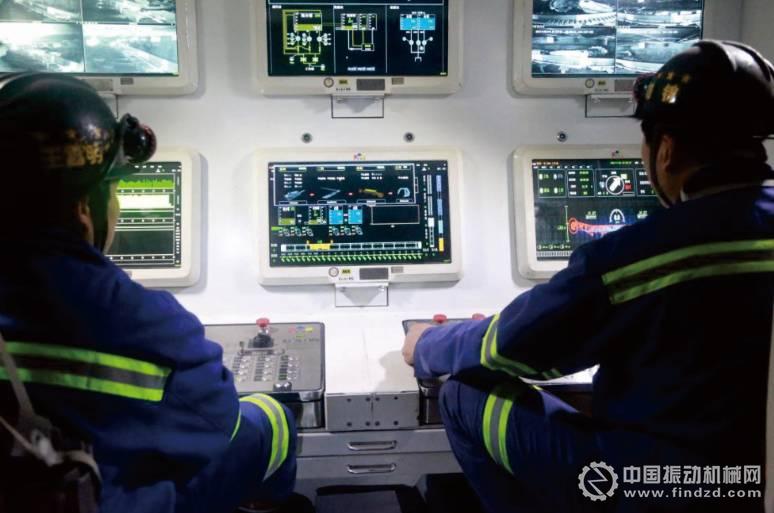
工作面順槽監控中心遠程采煤

調度指揮中心全景
如今該礦中厚煤層智能化無人綜采工作面實現了生產期間工作區域由原來9人聯合操作(煤機司機3人、支架工5人、運輸機司機1人)減至1人巡視。通過智能化無人綜采工作面兩順槽超前支架升級改造,由原來的24人單體支護減至12人遙控操作,并且具備了自動化遠程控制功能。
除了達到“機械化減人”的效果之外,效率也大大提升。黃陵一號煤礦應用的薄煤層智能化綜采工作面,有的地質條件差、煤層分布不均、且時有夾矸現象,但依然創造了單班連續開采8刀的記錄,月生產能力穩定保持在23萬噸以上,其中2016年1月份生產原煤27萬多(單班5千多噸)。
怎么樣?看到這兒,是不是也和小編一樣想感嘆一下:事實告訴我們,“無人化開采”這個曾經不敢想的事情離我們真的越來越近!
02 同忻煤礦
同煤集團和國電電力共同出資的股份制企業,是山西省和同煤集團“十一五”期間的重點工程之一,也是塔山工業園區主力生產礦井之一,設計生產能力為1000萬噸/年。
2013年8月,由同煤集團承擔的國家發改委“同忻煤礦千萬噸級高效綜采關鍵技術創新及產業化示范工程”項目立項。2016年7月,8202綜采面被選定為試點,經過井下安裝調試,進入試運行階段。
該項目的實施使設備替代工人進行井下開采,實現地面及井下控制中心對設備的智能監測和集中控制,大大降低了工人勞動強度,將工人從危險的工作面采場解放到相對安全的順槽監控中心。
現在采煤工只需坐在采煤工作面外的監控室,完成安全確認后,按下啟動按鈕,采煤機以預先設定的牽引速度,按設定的參數要求自動割煤,形成記憶截割模板,并在自動截割過程中不斷修正誤差。
同時,順槽監控中心還可對采煤機進行遠程實時監測的啟停控制,通過紅外線發射器和接收器,追蹤采煤機運行狀態,實時獲取采煤機位置信息,數據自動完成,上傳給順槽監控中心,遠程操作人員就可以獲得比就地觀測更好的效果!
當然,還可按照設定程序對工作面端頭的特殊開采,自動進行斜切進刀、割三角煤等工序……
不多說了,戳視頻了解一下吧!
目前同忻煤礦8202綜采工作面回采率達到85%以上,生產能耗降低5%以上,工作面瓦斯、煤塵及自燃發火防治均可實現安全可控;
同忻煤礦綜采二隊隊長說:“綜采隊原來每班20人,實現智能開采后,每班不到10人即可完成任務,而且效率提升了50%,減下來的工人主要負責安全巡檢和設備維護工作。”
小編想說,除了感嘆技術的進步,更為行業的進步感到自豪!
03 棗礦付煤公司
山東能源棗莊礦業(集團)所屬煤礦,是一座設計生產能力120萬噸/年的現代化國有重點煤礦,現已達到300萬噸生產能力。
這也是在智能化開采方面取得亮眼成績單的一所煤礦。
3上1008工作面是該礦一個6米大采高智能化工作面,集無線通訊系統、視頻監控系統和智能化控制系統于一體,目前已經實現了地面遠程控制的智能化生產模式,實現了地面調度指揮中心遠程操控‘一鍵啟動’高級功能,形成了‘可視化遠程干預’的安全生產新模式。
和同忻煤礦一樣,如今操作員只需坐在地面調度指揮中心,通過視頻監控系統完成安全確認后,按下“一鍵啟動”按鈕,將地面遠控操作臺模式切換至“全智能模式”,智能化軟件彈出工作面順序啟動提示界面,會按順序啟動泵站、皮帶、轉載、破碎、運輸機、支架跟機與采煤機。
地面工作人員通過采煤機遠控操作臺結合地面調度大屏工作面視頻信息,控制采煤機開始截割,液壓支架依據采煤工藝智能跟隨采煤機動作。
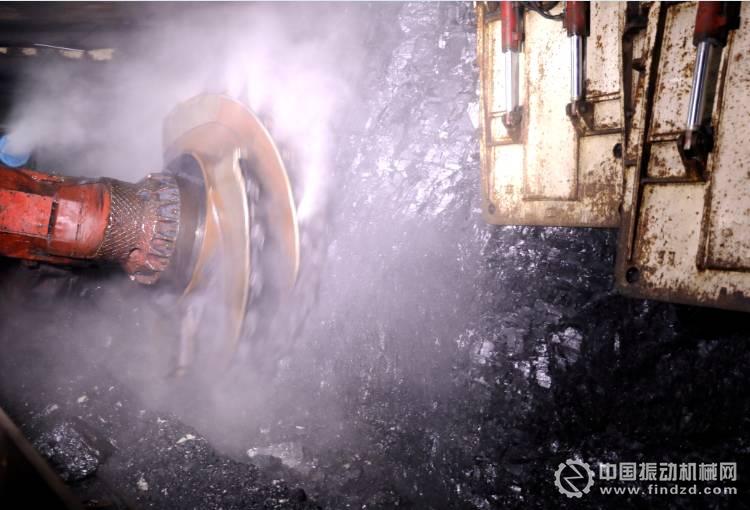
井下采煤工作面
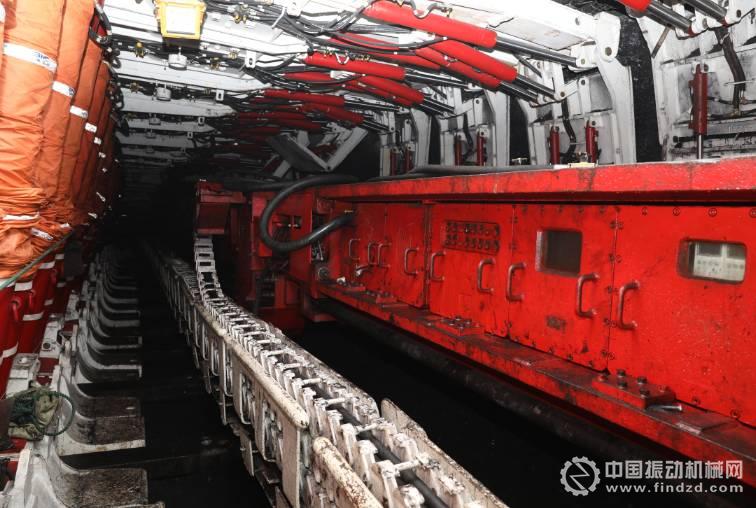
“有人巡視、無人值守”智能化開采工作面
現在該工作面回采率達到98%以上,生產能耗降低10%以上,工作面瓦斯、煤塵及自燃發火防治均可實現安全可控;
原來工作面正常生產需要12人,現在生產只需安排5人巡檢即可完成。
厲害吧?!小編除了想給一個大拇指外,還腦補到這樣一個畫面:
操作人員按下調度指揮中心總控臺啟動按鈕,400多米的井下工作面采煤機緩緩啟動,穩步前行,開始自如流暢地割煤、推溜、移架,滾滾的“烏金”就通過傳輸皮帶流水般奔向地面……
04 濱湖煤礦
山東能源棗莊礦業(集團)所屬煤礦,核定生產能力110萬噸/年。
傳統的薄煤層開采技術用人多、效率低、成本高,而且采機組現場自適應能力差,采高大了,容易割頂、底矸石,使矸石混入煤流;采高小了,容易丟煤,造成資源浪費。
濱湖煤礦“薄煤層可視智能化遠程割煤三機配套設備”則改變了這種情況,大幅降低了工人的勞動強度,減少了職業安全危害,將職工從危險性較高的區域轉移出來,從艱苦危險的環境和高強度體力勞動中解放出來。濱湖煤礦16108工作面和16115工作面都運行了薄煤層自動化無人開采機組。
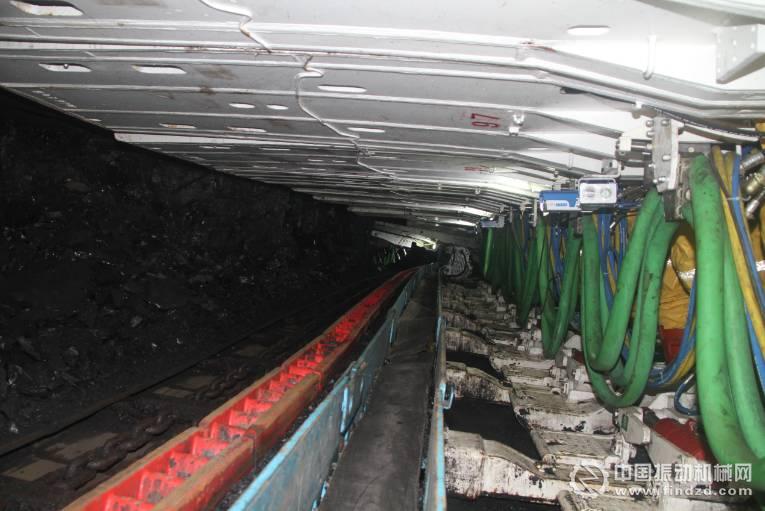
16115薄煤層自動化無人開采工作面
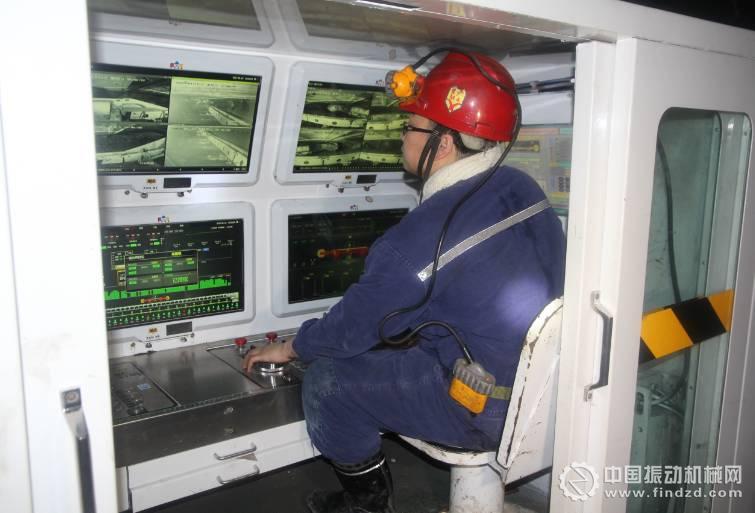
16115工作面材料巷集控中心現場操作
設備的成功運用以后,生產工序由原來的2名煤機司機跟機操作、6名支架工分段跟機拉架,變為1人遠程操控,2人工作面巡視。經過對工作面崗位進行重新核算,僅需60名職工,即可完成當天的正常生產,較傳統工作面減少崗位工67余人,勞動用工壓縮了50%以上,回采工效達每工48噸以上,人均工效增幅195%,年減少人工成本支出約900多萬元。(注:王奎供稿)
看!是不是綜采工作面“有人安全巡視、無人跟機作業”的夢想已經在這個礦實現了?!而且讓“機械化換人、自動化減人”的理念得到實踐,更從源頭上實現了“無人則安”。
05 紅柳林煤礦
陜煤集團控股煤礦,設計生產能力1500萬噸/年。
2011年,第一個7米大采高綜采工作面投入生產;
2012年,首次在15205綜采工作面進行了信息化與機械化綜采的“兩化”融合嘗試,與北京天瑪公司聯合攻關完成了綜采成套裝備智能系統;
2014年,作為“全國煤炭行業‘兩化’深度融合型智能礦山現場會”重要的主會場之一,大采高智能化綜采工作面的嘗試,得到了同行業高度評價;
2015年,成為全國煤礦智能化無人開采技術的試點示范單位;
2016年,25207智能化綜采工作面正式開工建設……
這些耀眼的成績單勝于一切語言的描述。智能化、無人化開采,就這么轟轟烈烈的在紅柳林煤礦開展著。
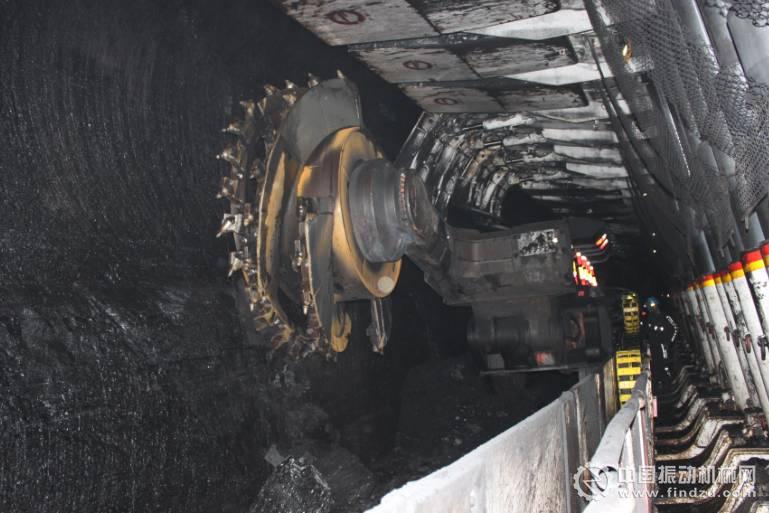
具備年產千萬噸生產能力的綜采工作面
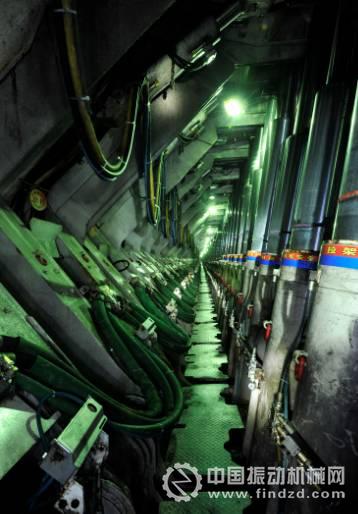
七米大采高綜采工作面液壓支架
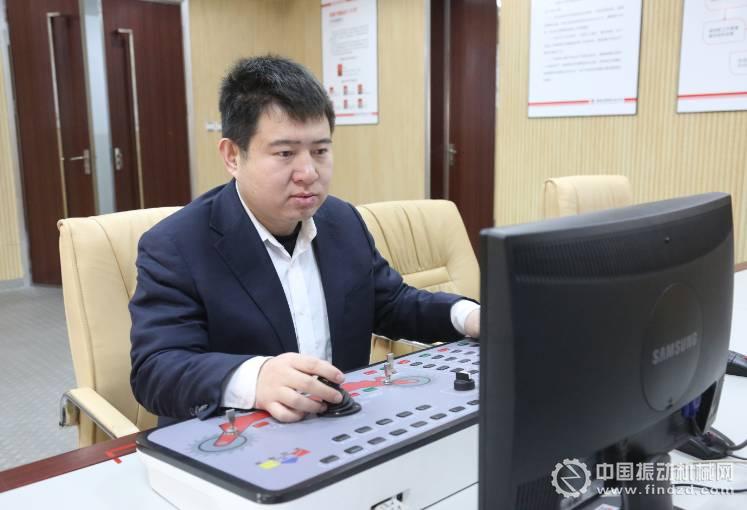
工作人員操作智能化綜采工作面地面遠程遙控操作控制臺
現在,只需要這樣錯做即可完成采煤: 開機前,首先由地面操作控制臺人員跟井下煤機司機取得聯系,查看是否具備開機條件;如具備,將由地面控制臺發送一鍵啟停指令,隨即三機、泵站一鍵啟動后,煤機開啟,采煤工序進入自動化跟機狀態,完成割煤、移架、推溜等生產工序。采煤過程中,根據不同地質構造,設備如有跟進不及時的情況,井下采煤機司機將對整個自動化跟機狀態進行人為調整,支架工為丟下的支架進行人工補架。即可完成整個工序。
通過嘗試,紅柳林礦業公司智能化綜采工作面現已進入了末采階段,預計2017年12月底,可完成首個智能化綜采工作面的采煤任務。
小編已經忍不住的想說:讓技術進步來的更猛烈一些!讓“無人化”開采來的更早一些!
06 轉龍灣煤礦
兗礦集團在內蒙古首對自主建設的特大型礦井,兗礦集團“十大骨干礦井”之一,目前正處于試生產階段,設計生產能力500萬噸/年。
今年3月份,轉龍灣煤礦通過了中國煤炭工業協會組織的專家,對“3-4米煤層千萬噸級智能化綜采裝備關鍵技術研究”科技成果的鑒定。
當時專家就認為,該項目首次在3-4米煤層條件下達到年產千萬噸級的水平;在國內綜采工作面首次采用LASC技術研發了設備運行軌跡檢測技術,實現了液壓支架與刮板輸送機自動校直,可在復雜條件下實現工作面自動化生產模式常態化運行。
首次在國內研制出具有慣導特性的智能化采煤機,行走位置控制精度±3cm,滾筒截割高度穩態重復精度±4cm,截割牽引速度大幅度提高,實現了全作業循環的自動化。
工作面支架、端頭支架、超前支架自動協調控制系統,可遙控超前支架。
設備列車自動、柔性、快速自移,實現了工作面整體協同推進;研制了智能變頻調速的大運量、高可靠、超重型刮板輸送機,鏈速匹配控制精度大幅度提高,運行能耗大幅度降低。
研制了千兆因特網主干、無線WiFi多級跳傳輔助的智能化綜采裝備的綜合通信平臺。
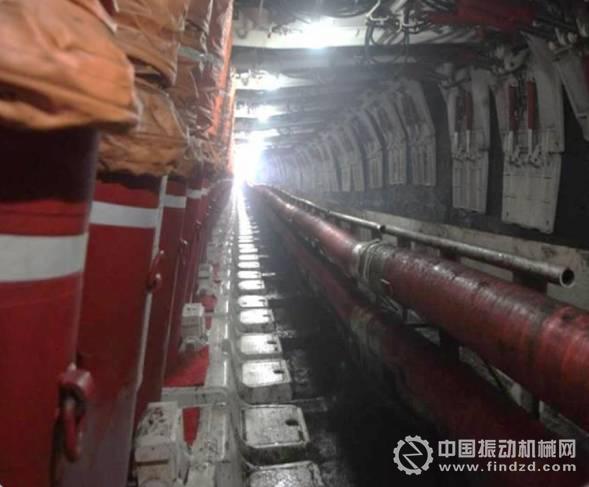
井下工作面
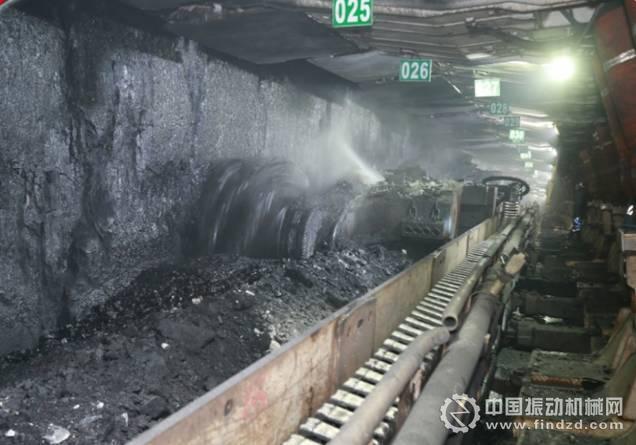
采煤工作面
自智能化工作面運行以來,實現了最高日產3.78萬噸,最高月產90.13萬噸,達到1000萬噸/年能力,實現了高產高效的目標;
每班可減少操作工人5人,綜采隊建制可減少20人,實現了“機械化換人、智能化減人”的目的。
看,“無人則安,少人則安”,“機械化換人、自動化減人”不僅僅是停留在口號上!
07 新元公司
陽煤集團所屬煤礦企業,屬陽煤集團主力礦井,年設計生產能力300萬噸/年。
自2011年9月正式運營以來,新元公司就以建設機械化、自動化、信息化、智能化的一流礦井為目標。
2012年10月18日,陽煤集團公司第一套綜采自動化工作面就落戶新元公司。
如今,新元公司已擁有7個綜采自動化工作面。工作面工作的人少了、效率提高了、成本降低了、支護質量改進了、安全系數提高了、勞動環境改善了……如今的新元公司,已經實現了瓦斯濃度與采煤機速度聯動控制、采煤機自動截割三角煤、采煤機記憶切割等12個版塊自動化,地面變電站、主扇、瓦斯抽采泵站,井下中央配電室、水泵房等崗位的無人值守。
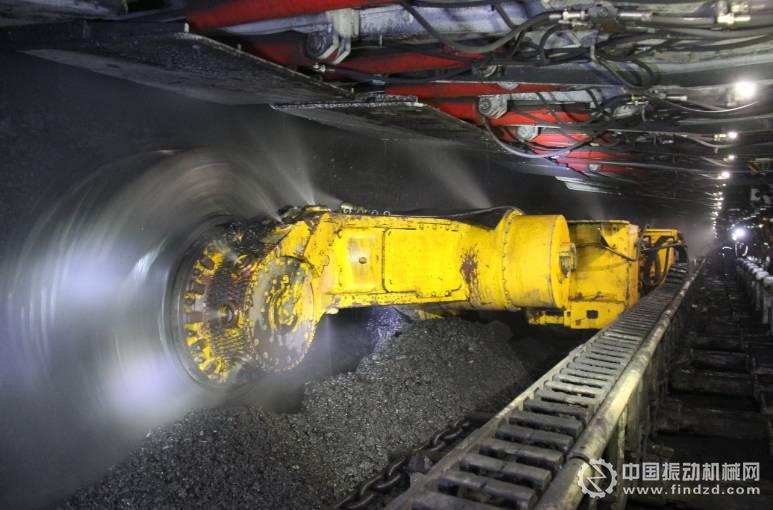
自動化綜采工作面生產組織
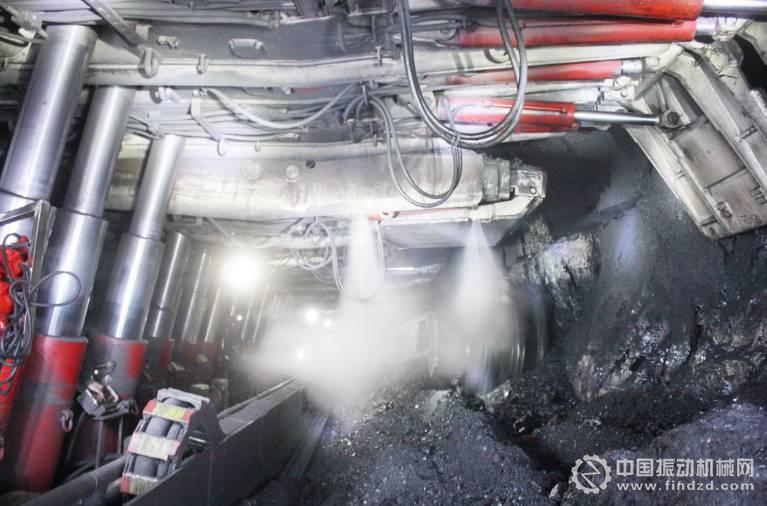
自動化綜采工作面支架自動降、移、升及推溜和噴霧
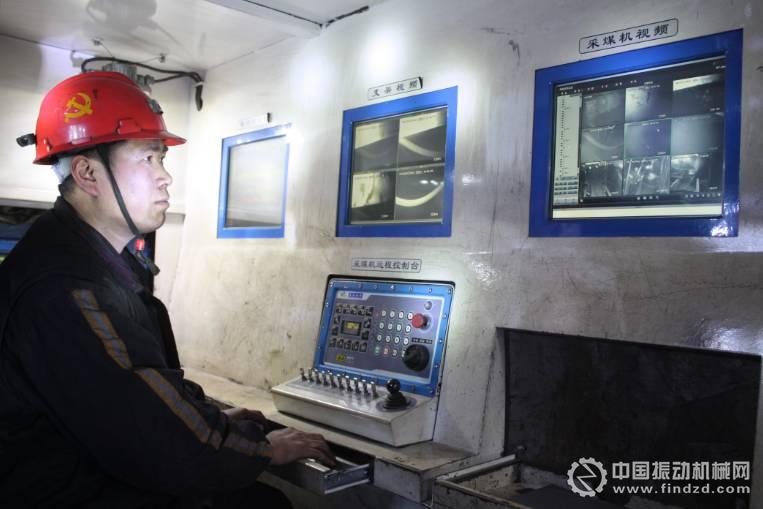
自動化綜采工作面井下主控制室
要說取得的效益,咱們以新元公司3108工作面為例說一說:
原用工165人,實行自動化工作面后用工變為94人,共減員71人。原工效32.071噸/工,應用自動化綜采技術后工效54.704噸/工,工效提高了22.633噸/工,提高幅度70.57%。
材料成本下降明顯,噸煤成本降低4.08元/噸。自2016年12月至今,3108工作面材料成本降低1092.06萬元。
人工成本費用減少568.2萬元。3108工作面安裝調試后,生產人員因自動化工藝實際減少71人,月度減少職工薪酬費用47.35萬元,共減少人工成本568.2萬元。
08 巴彥高勒煤礦
山東能源淄礦集團所屬煤礦,設計生產能力1000萬噸/年。
巴彥高勒礦,這個按照“國際先進、國內一流”標準投資建設的煤礦,實際運行情況,和他的投建標準一樣,保持著現代化水平。
自2013年建成實現聯合試運轉以來,巴彥高勒煤礦憑借先進的現代化設備和精良的員工隊伍,實現了智能化開采和自動化生產。
當然,作為新建礦井,巴彥高勒煤礦在智能化開采這條路上,也走過一條異常艱難的道路。不過,最終還是迎來了智能化的全面推廣和應用。
目前,該礦還在全工作面液壓支架自動跟機操作、成套綜采裝備智能系統創新應用等自動化核心技術方面取得了初步進展。
聽說,下一步,該礦還將在無人跟機作業、數字化信息上報等方面加大投入,持續為礦井實現減人提效和安全高效提供便利條件。
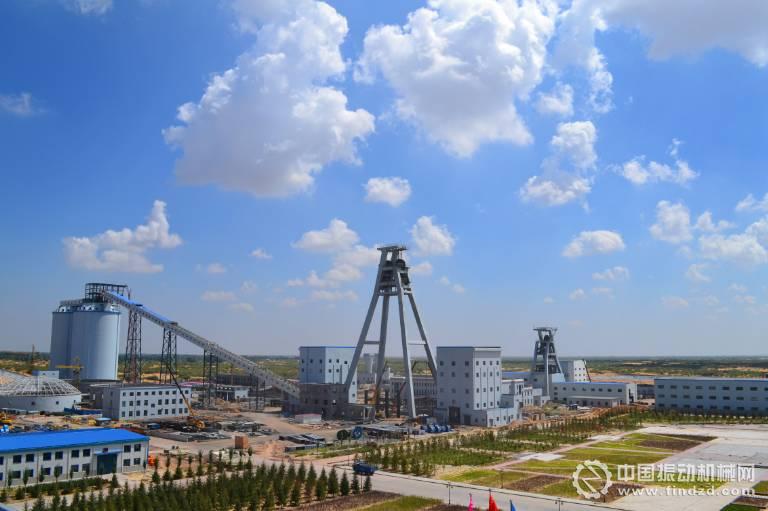
巴彥高勒煤礦全景
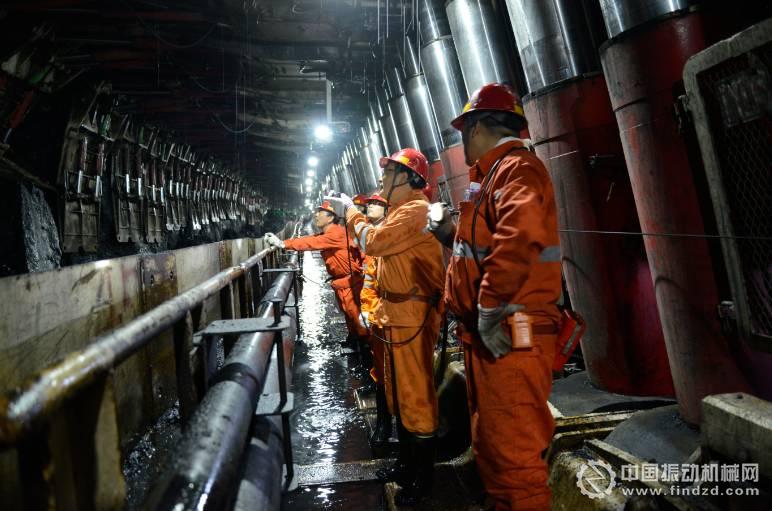
管理人員在查看智能工作面運行情況
現在,巴彥高勒煤礦已經可以在地面的智能監控中心實現遠程監控和操作,人員使用率減少了25%,效率提高了近20%,智能化開采也已經達到了國內領先水平。(注:弋永杰供稿)
一個字,
09 金鳳煤礦
神華寧煤集團主力生產礦井之一,年設計生產能力400萬噸/年。
這是一個被稱為“智慧礦山”的企業,也是一個薄煤層開啟智能化開采的煤礦。
金鳳煤礦薄煤層占可采儲量的34%,平均開采厚度不足1.5米,井下開采難度大。
經過多年研究與摸索,金鳳煤礦同時引入自動化開采及柔膜混凝土沿空留巷兩項技術,并于2016年在部分薄煤層工作面正式應用。
煤礦生產過程中,采煤與掘進的配比關系,直接關系到采掘接續問題,進而影響礦井的正常平穩生產。但在實際開采過程中,二者很難保持一種均衡狀態。柔膜混凝土沿空留巷技術就是金鳳煤礦為緩解生產接續緊張實施的有效措施。今年下半年,金鳳煤礦又在某綜采工作面實施了“切頂卸壓自動成巷”技術。這樣既可以大幅降低綜采工作面掘進成本,又大大提高了資源回收率。
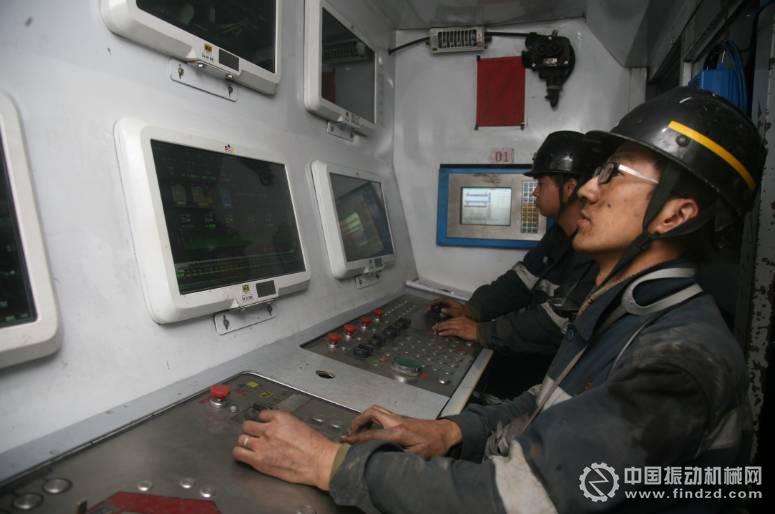
技術員在控制臺操作
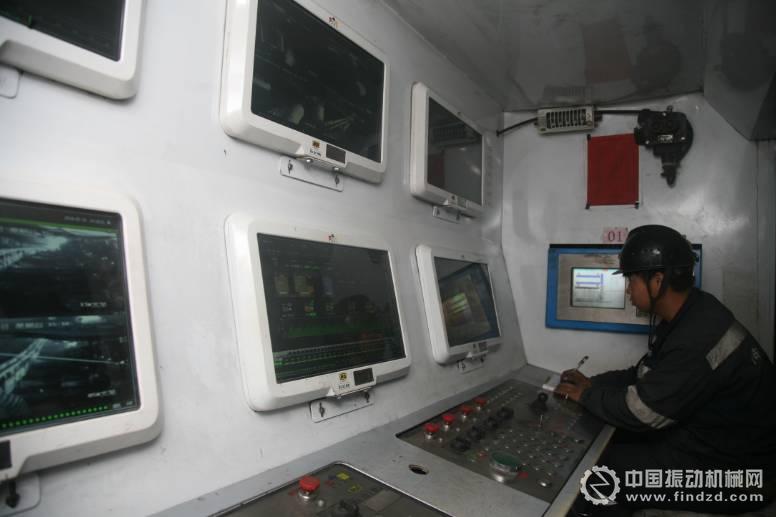
控制臺司機記錄工作面數據
“智慧礦山”建成后,調度室變成了各類生產設備的總控室,采掘、運輸等工作均可一鍵完成。
“智慧礦山”建設給礦工帶來了福音,自大量使用自動化設備和新技術以后,該礦職工比以前輕松多了,可以輪流上崗,休息時間也多了。
現在走進金鳳煤礦總調度控制室,井下生產工作情景在電子大屏幕上一覽無余。
小編認為,這些是所有煤礦未來的發展方向,也是礦業發展的未來目標:建設智慧礦山,實現智能采礦!
10 張集煤礦
淮南礦業集團主力礦井之一,安徽省第一座千萬噸級井工礦井,核定生產能力1240萬噸/年。
在高瓦斯突出煤層“三軟”地質條件下實現智能化開采的煤礦屈指可數,張集礦就是其中一家。2015年張集煤礦選定地質條件不好的1312(1)工作面為試點,開展中厚煤層智能化開采的探索。
現在走進1312(1)工作面,一排排支架整齊有序,LED燈照得雪亮,巨大的煤機揮舞著手臂切割煤壁,瞬間煤流傾瀉而下,沿著輸送機向前流走。
目前,1312(1)工作面建立了以液壓支架自動跟機動作為主、人工遠程干預為輔,以綜采運輸設備集中自動化控制為主、人工遠程控制為輔的自動化生產模式,做到了無人跟機作業、有人安全值守。地面調度室和井下順槽監控中心可對工作面采煤機、液壓支架、泵站等進行遠程控制、監測、數據上傳、故障診斷等。
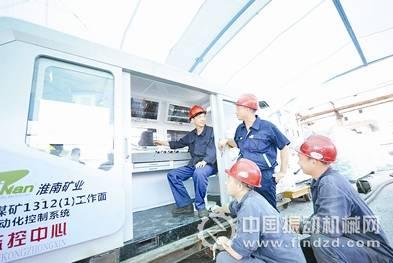
1312(1)工作面綜采自動化控制系統監控中心
人員也大幅減少。據了解,該工作面綜采二隊每個作業班已經可以至少減少9名作業人員:2名系統工、4名端頭工、3名支架工。煤礦生產一線告別了人海戰術、貼身戰術。
小編知道,這些不代表全部,還有很多煤礦已經實施或者正在探索礦井智能化、無人化技術;不僅在北方的現代化礦井,還有很多南方的煤礦都在積極研究或正在上馬。
其實,從嚴格意義上講,目前智能化無人開采并未完全實現工作面落煤區域的絕對無人,但專業人士表示,如今的發展程度有兩點重要效果:
一是將工人從操作工變成巡視工,由設備的自動化替代人工勞動,大大降低了工人的勞動強度;
二是將工人從危險的工作面采場解放到相對安全的順槽監控中心,在監控中心對設備進行遠程操控,提高了工人工作的安全系數。
以最典型的井下支架操作工來說,以往一個工作面需要3到5名支架工,采用智能化無人開采技術后,液壓支架實現自動跟機連續推進,可完全替代工人操作,僅需1人在工作面進行安全巡視。
據了解,我國煤炭智能化無人開采技術從2010年起分別經歷了可視化遠程干預(1.0時代)和工作面自動找直(2.0時代)兩個技術階段,目前正處于向透明工作面(3.0時代)研究過程中,并最終進入透明礦井(4.0時代)的技術階段,實現煤炭無人化安全高效開采的目標。