原料廠燒結車間成品篩分系統,是根據生產需要將經熱破和冷卻后的燒結礦,利用振動篩將不同粒級的燒結礦分選出來,是燒結生產過程最重要的環節之一。整粒的好壞直接影響到成品燒結礦的粒度組成,影響到返礦和鋪底料的質量,進而影響到高爐正常生產。
傳統的燒結篩,在結構上存在一定的缺陷,出現故障時需啟動備用設備,倒鏈板機機頭翻板進行倒篩作業。長期以來,倒篩作業時需停鏈板機,進入機頭溜槽內進行割焊作業,不僅危險系數大,倒翻板降料層外翻生產設備故障率也高。另外后期倒運外翻料工作量大,影響生產的同時也增加了員工勞動強度。
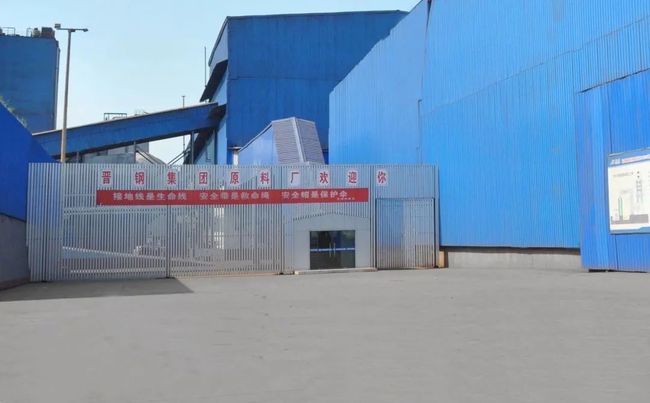
為解決這一難題,晉鋼集團維修技術骨干從優化生產工藝入手決定對損壞的篩分系統進行維護改造。經多次現場研模調試,利用檢修時間將鏈板機下料口溜槽舊翻板割除,調整溜槽角度至合適狀態,在下料口處制作密封罩和支架,成功解決了倒翻板需人工調試、耗時長的弊端。改造后倒篩作業,只需將其中一條線的鏈板機下料口堵滿,料會自動流向另一個溜槽,與之前的倒翻板作用一致。
改造實施后,篩分系統倒篩既不用停鏈板機,也不用降料層外翻生產,節省了大量的人力物力財力,為成品系統的生產順行起到了很大的促進作用。